Contributed by: Sciemetric Staff

Faulty applications at the dispense station can cause major problems in the field. Unfortunately, dispense is also one of the most complex processes on the manufacturing line to effectively monitor for quality assurance.
Due to the fluid nature of the dispensed materials, faulty applications can go unnoticed until it is too late. Issues with a poor or faulty dispense may not crop up until later in the production process (or worse, in the field), when they are likely more costly and troublesome to identify and address.
One of the most troublesome dispense quality issues is trapped air that has led to bubbles in the dispensed material. The void created by the bubbles can weaken an adhesive or lead to failed leak tests downstream.
Bubbles can be caused by a variety of mechanical problems such as partially blocked, bent, or incorrect nozzles and process variations in pressure, temperature, time and viscosity—making it necessary to monitor a variety of parameters to ensure a proper dispense operation, every time.
Quality monitoring dispense operations
By monitoring the right dispense parameters and collecting and analyzing the right data from the dispense process, quality issues can be caught and addressed before parts leave the dispense station. Digital process signature analysis has repeatedly proven itself ideal for this purpose for a broad variety of dispense operations.
First, the dispense station must be equipped with digital sensors to capture pressure, time, amount of fluid dispensed, bead width and any other parameters that may be important to characterize the quality of your specific dispense operation.
These data points can then be plotted as a waveform, or signature, which provides the clear and immediate visual evidence of whether the dispense operation was completed within spec (see below examples of waveform overlay). When datapoints deviate outside of the acceptable, set limits for the test or process, the application is flagged as faulty.
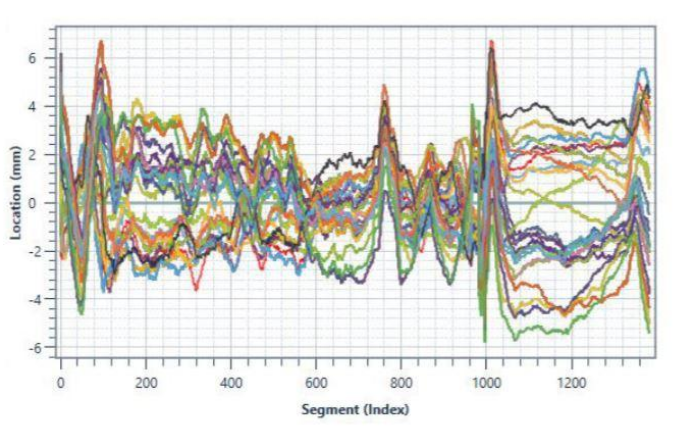
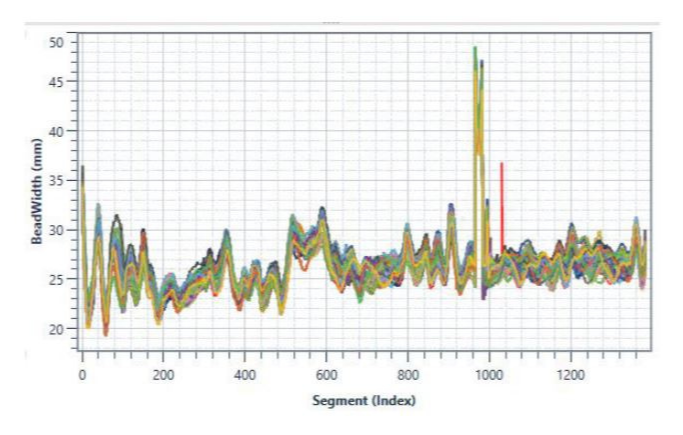
So how do you identify the proper parameters to monitor and ideal limits to set during your dispense operation? You must take into account every possible variable of your dispense operation. We’ve listed these considerations below.
10 factors to consider to effectively monitor dispense operations
- Type of media being dispensed (sealant, coating, adhesive)
- Is it anerobic (cures when parts are put together and lack of oxygen), or does it cure in presence of air (let cure before parts are put together)?
- Is the dispense for a linear bead, a spot, a blob or a drop of material? Signature analysis can quality assure all of them. But the system must be configured appropriately depending on whether it will measure a trace going around a determined path or just a blob of material at a joint, for example
- If the operation is dispensing a linear bead, is it continuous or is it segmented to bypass areas where no media is desired? If you are dispensing a linear bead, you must also identify the desired height and width of the trace
- What is the temperature of the part upon which the media is dispensed? This can impact spread or flow of the media
- The time available for the dispense operation to complete to keep pace with production. This affects mm or inches per second rates, as well as part per hour rates
- The estimated nominal pressure at dispense tip. Deviations in pressure are one of the most telling indicators of a quality issue, such as clogged nozzles and hardened material
- Type of dispense equipment and media supply. Factoring this into the equation is critical to understand when a deviation from the accepted norm for a “good” dispense operation may be related to an equipment or supply issue
- Whether the dispense system is hosted by a PLC or manually triggered by an operator. The potential for manual error by an operator must be considered and compensated for
- Physical size of the part. Some medical devices, for example, are very small. The smaller the bead and the smaller the total dispense area, the higher the risk of blockages or incorrect widths and the less margin for error
Want to learn more? Read our Application Note on In-Process Test & Monitoring: Dispense Operations to learn more about process signature analysis can boost the quality and reliability of your dispense station. Or contact our team to discuss how in-process testing and monitoring could be employed on your line for better defect detection at the dispense station.