Contributed by: Sciemetric Staff
So, your plant collects data—but how are you using that data? Is your data empowering individuals on the plant floor to take quick, decisive action? Is your data supporting timely and informed decision-making in the corner office?
With reams of manufacturing process data being generated every day from each part and assembly on the production line, smart manufacturers are becoming wise to the power their data holds. Through meaningful data collection and analysis, smart manufacturers are experiencing profound gains in overall yield, product quality and process optimization.
Here are five trends smart manufacturers are implementing today:
1) Breaking down data silos
Data from process and test stations is no longer being left stranded on local servers or someone’s personal laptop.
Smart manufacturers are collecting data from every station up and down the line, as well as the repair bay, digitally connected over a robust network architecture so that data is made accessible to decision-makers across the enterprise.
By breaking down data silos across the enterprise, everyone has access to an individual birth history record for each part or assembly on the line, indexed and cross-referenced by serial number for quick retrieval when it’s needed.
2) Collecting the right data
The most useful form of data is the digital process signature, or waveform, that is generated by each cycle of a production process or test. Scalar values from SPC tools are useful in indicating a major production problem or flaw in the line, but it’s the process signature data that allows you to drill down to pinpoint small deviations in the production process for a specific part or assembly and trace the root cause of a problem.
Machine vision images and the related data are also important elements in tracing root cause. Smart manufacturers have equipped their process and test stations with the digital technology to collect these important forms of production data in one accessible database.
3) Analyzing the data
Smart manufacturers realize that data left to sit in a database is worthless. You have to make your data work for you. Those invested in taking advantage of Industry 4.0 are investing in big data management and analysis tools that visualize their findings in a manner that lends itself to easy understanding—even by the non-engineer.
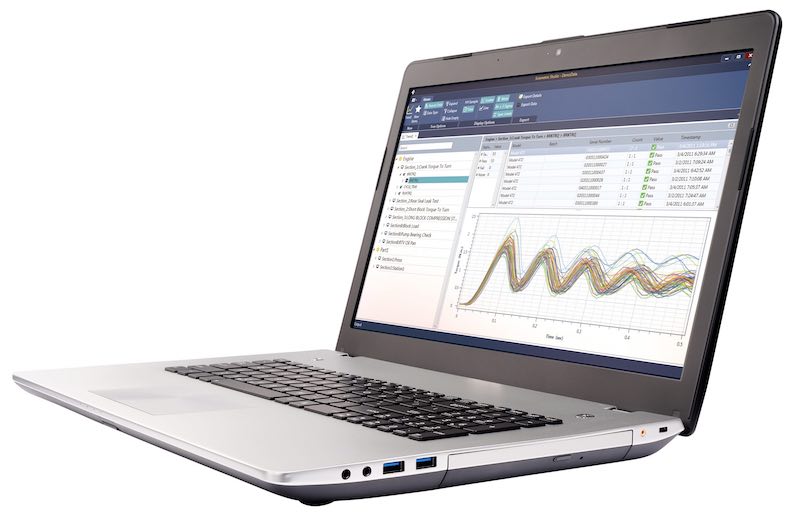
4) Acting on the data
Smart manufacturers that have implemented routine data analysis into their production line also have a process in place to act on the insights yielded from data analysis.
When gaining insight in production real-time (which we define as within one cycle of cycle completion for any process or test on the line), manufacturers have the ability to spot process anomalies and variations that impact key performance indicators promptly after they have occurred. This allows quality engineers, managers and even individual operators to act fast to address any problems on the line at an early stage.
5) Driving continuous improvement
The beauty of having the right data and analysis at your fingertips is that you can take a more proactive approach to product quality. Quality engineers use their data to find trends and patterns that reveal the “how” and “why” of decreases in yield and quality, then apply refinements to test limits or other upstream quality control benchmarks. This gives smart manufacturers the insight to improve quality, reduce scrap, rework and warranty claims, and bring new lines and new plants online much faster and economically than ever before.
Achieving the ‘Model of One’
All this leads to achieving the ‘Model of One’, where your line has the real-time insight to track and pluck a single defective or suspect “needle in a haystack” at any time, whether it’s a single component part or an assembled product, like an automotive engine. Implementing these strategies that allow maximum insight into your production line at any given time is becoming a standard requirement in smart manufacturing.