Contributed by: Sciemetric Staff
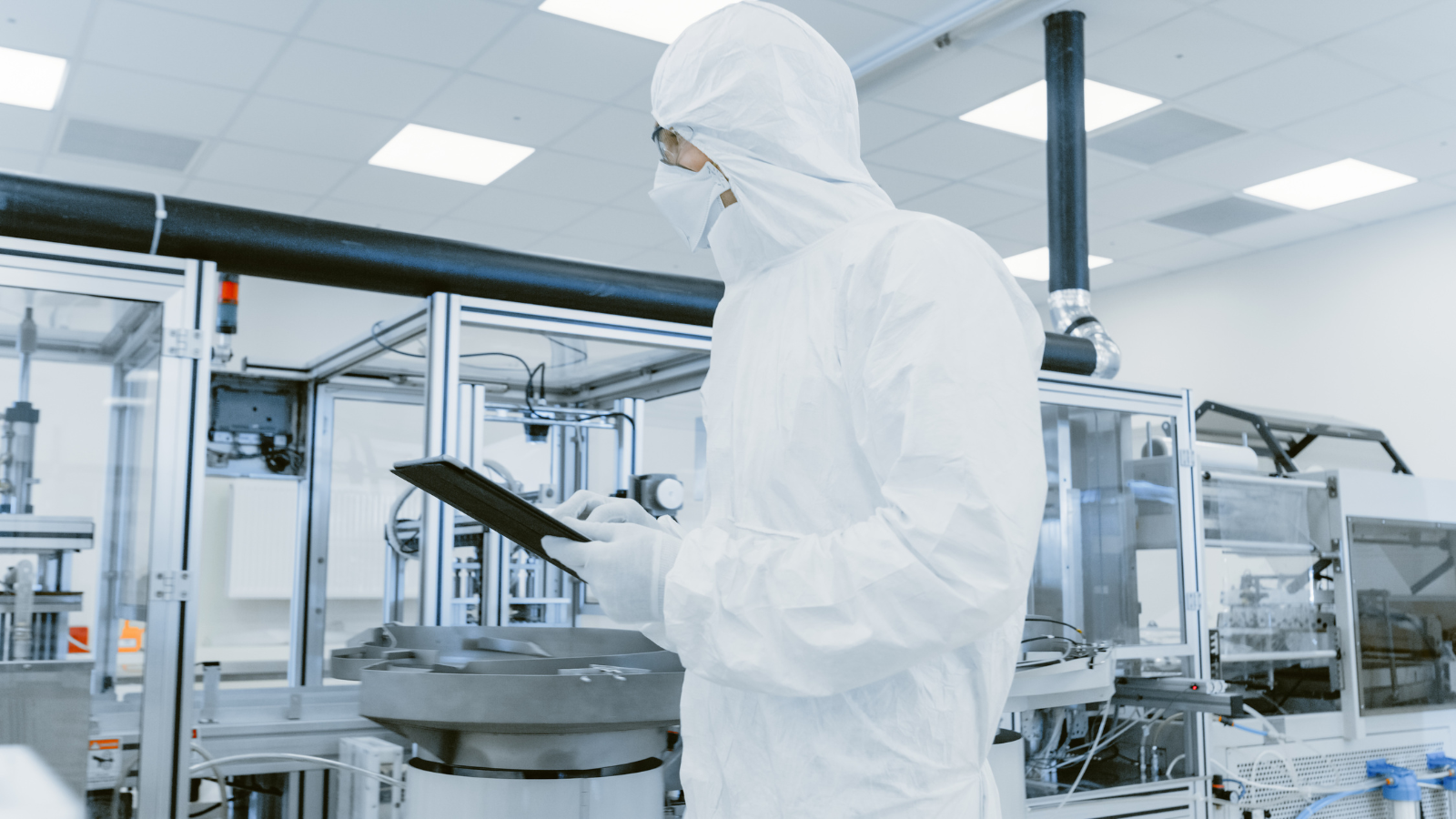
Historically, medical products have been manufactured in batches or lots, with a sample of the devices evaluated for quality using destructive, visual, or audit testing. More recently, however, we are seeing a paradigm shift.
With more and more medical device manufacturers taking advantage of the benefits of measurement and data management technologies on their lines, the result is a movement away from destructive end-of-line sample testing and towards non-destructive testing systems. Medical manufacturers are realizing the benefits of using in-process testing and process monitoring to catch production defects in real-time, on a part-by-part basis.
By analyzing the data gathered from your critical-to-quality processes, it becomes possible to develop a detailed understanding of the underlying physical processes, and how these process variables interact to affect product quality. This approach provides a number of key benefits, including reduced product costs and improved manufacturing efficiency, as well as improved product quality, traceability, and risk mitigation.
CONTACT US TO ENABLE NON-DESTRUCTIVE TESTING ON YOUR LINE >
Implications of the Destructive Testing, Sample Testing Approach
As mentioned above, the traditional approach to ensuring product quality has been based on testing a statistically representative sample of parts from each batch. Tests are designed to evaluate whether the samples meet product requirements, both from a function and performance perspective, as well as for reliability and durability. However, due to the nature of this testing, many parts are destroyed during this process.
Based on the results of these sample tests, the failure rate of the remaining parts is statistically estimated. If the estimated failure rate is above acceptable limits, the entire batch is removed from production, quarantined and, in many cases, scrapped.
The effectiveness of this approach relies strongly on how well the process is controlled, as it is assumed that the failure rate of the test sample is representative of the entire lot. The less controlled the process, the larger the required sample size, and the higher the cost of the testing. This includes the labor and capital costs associated with the performance of the test, as well as the cost of the sample parts that are destroyed in the test, the vast majority of which could be defect-free.
However, though we know that a well-controlled process is critical to controlling costs, unfortunately, without a means of directly monitoring the performance of the manufacturing process, maintaining this level of control is very difficult and prone to subjectivity, making this test approach problematic.
Benefits of a Non-Destructive Testing, Data-Enabled Approach (In-Process Testing & Monitoring)
The alternative to destructive sample testing at the end of the line is to collect data during your critical-to-quality processes. This represents a fundamentally different approach to managing risk and instills quality directly into the manufacturing process. Instead of relying on batch sample data, each part is evaluated individually, increasing the test coverage to 100%.
Since data acquired during manufacturing can be correlated to the precise step where the defect was created, this approach ensures that defects are caught before they get to the end of the line, when they are most cost-effective to fix. It also ensures that the quality of the manufactured product is controlled and maintained on a continuous, on-going basis.
Also, by consolidating and storing all the in-process test data associated with each part, it becomes a vital component of the device history record.
CONTACT US TO ENABLE NON-DESTRUCTIVE TESTING ON YOUR LINE >
How to Implement Non-Destructive Testing for Medical Device Manufacturing
The first step in implementing an in-process testing approach is identifying the critical steps in the manufacturing processes. For each of the critical processes, you must identify which parameters should be monitored to provide the best indicators of product quality, and then apply measurement tools to feed this data into your system.
By monitoring and analyzing the critical data points in real-time, defective parts are identified and rejected on the production line, before continuing to the next step. This provides the advantage of detecting defects as they happen, allowing defective parts to be removed from the process as early as possible. This improves the efficiency of the manufacturing line, since resources at subsequent steps are not wasted on parts that are already defective. Furthermore, the in-process data provides critical feedback that can be used to control and optimize the manufacturing processes during production.
Once the in-process tests results have been validated against the destructive end-of-line tests, it is possible to eliminate them without any loss of product quality. Instead, quality is guaranteed by monitoring, analyzing, and recording the in-process data on each part as it is being manufactured. This represents a profound change in the way product quality is controlled. The end results are significant cost savings both immediately and in the longer term.
CONTACT US TO ENABLE NON-DESTRUCTIVE TESTING ON YOUR LINE >
Results After Implementing Non-Destructive Testing for Medical Device Manufacturing
When you implement non-destructive testing, no longer is it necessary to destroy 5-10% of the manufactured parts, the vast majority of which would pass requirements. In most cases, this cost savings alone is enough to generate 100% payback within the first year, if not sooner.
Product costs also decrease over time due to continuous improvements on the production line, leading to higher yields. This is accomplished by optimizing and controlling all of the critical manufacturing processes based on the real-time feedback provided. SPC analysis can now be based on individual parts, instead of batch-based data, providing more accurate statistics and more rapid feedback. In essence, this is equivalent to reducing the batch size from thousands down to one.
The operator costs of manual destructive testing are also eliminated. And the fundamental shift away from end-of-line sampling to 100% in-process testing ensures a higher level of product quality, which in the long run is guaranteed to save manufacturing costs overall.
Want to learn how to implement non-destructive testing on your medical manufacturing line? Contact us.
In the end, the combined advantages of a more cost-effective, higher-quality product provide the competitive edge necessary to succeed in today’s competitive medical devices market. Our specialists would be happy to speak with you about any challenges you’re facing and how in-process testing could be implemented for major improvements on your line.
See below, a couple of examples of how we've helped medical manufacturers
eliminate destructive pull-tests on their implanted devices production lines:
⦁ Crimp & Stake Verification >
⦁ Weld Resistance Monitoring >