Contributed by: Sciemetric Staff
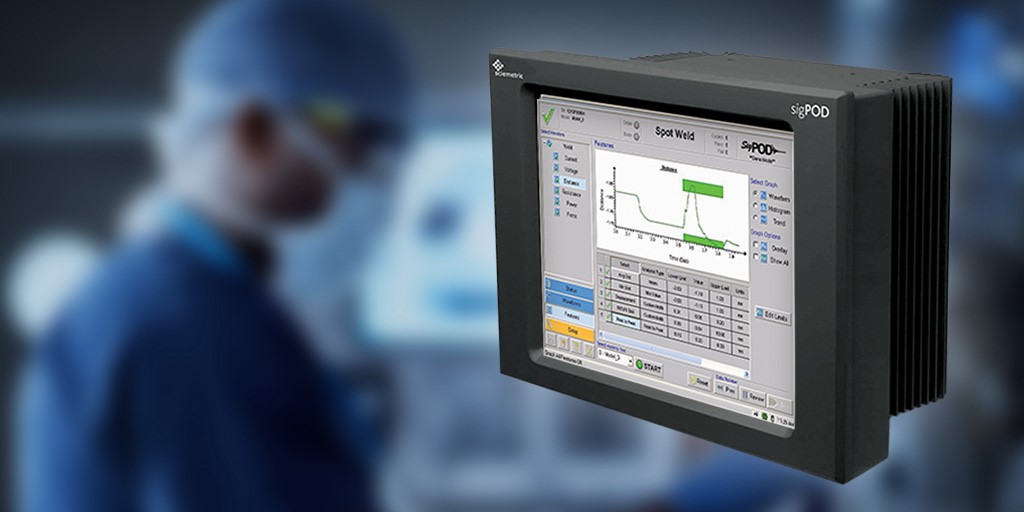
Pull-tests for welds on the production line are costly and provide no guarantee that defective assemblies won’t slip through.
For medical device makers faced with the need to contain costs and deliver 100% quality assurance, what is the alternative?
Consider a pacemaker.
A pulse generator – a small metal vessel that houses a battery and electrical circuitry for regulating the heart with electrical pulses, is embedded under the skin. Leads (aka electrodes) run from this generator into a chamber or chambers of the heart to deliver those electrical impulses.
Key to the long-term and reliable function of the device is the connection between the leads and the pulse generator. This connection is commonly achieved through resistance welding. It’s imperative to ensure the integrity of this welded joint. Poor joints can fail unexpectedly, with fatal consequences for the patient. Such quality issues obviously pose a substantial legal and regulatory risk to the manufacturer.
The traditional approach to testing the integrity of this weld is destructive pull-test, with its obvious shortcomings. Perfectly good assemblies may be ruined, while faulty ones can still slip through and be shipped for use. Statistically predicted failure rates can be skewed if a process has drifted out of control or if the sample size isn’t large enough to accurately represent the lot characteristics. When an issue is found, an entire lot of assembled units must be recalled and scrapped because there is no data trail with which to zero in on only those units that are likely to bear the defect.
A better way to catch weld defects
We know how and why a resistance weld can result in a poor joint that’s prone to failure:
- If the metal is overheated and bursts out of the weld zone (an expulsion)
- If there is too little force for sufficient contact between the two metals to form a proper bond
- If there is too much force, which reduces the interface resistance for the weld
- If the materials are burnt (oxidized) from too much energy exposure
- If there is too little energy exposure for a sufficiently strong bond
- If the electrode is oxidized (dirty) or otherwise damaged
With digital process signature analysis, all the metrics that identify these issues – voltage vs. time, current vs. time, force vs. time, distance vs. time, electrical power vs. time, resistance vs. time and force vs. distance – can be measured, captured, profiled and plotted as waveforms for accurate visual analysis.
All this data can be collected and stored for each process cycle at the weld station in real time, even if the process takes only milliseconds to complete, recorded by the serial number of the part assembly in question.
Armed with this insight, the manufacturer can guarantee that every weld on every unit, whether it is a pacemaker or another medical device, is robust and reliable.
Download our Application Note, Avoiding Destructive Pull-Tests for Weld, to learn more about how the Sciemetric sigPOD with Process Signature Verification (PSV) software can be used to eliminate destructive testing at the weld station, reducing costs as well as boosting quality and dramatically reducing the risk of critical field failures.