Torque testing and torque monitoring helps manufacturers find the hidden problems in their process
Fasteners, such as nuts or screws, or an assembly such as an electric motor utilize torque to turn. A failure or defect in the fastening operation of something, even as simple as a fastener or small part, can affect the operation of an entire motorized assembly. In torque testing for manufacturing, the amount of force applied to move an object is measured and analyzed for comparison to a baseline. Any anomalies in torque characteristics can indicate a quality issue. With the right technology, you can use these anomalies to trace the root cause of a variety of defects.
We developed Sciemetric's off-the-shelf-technology to help manufacturers improve torque testing processes and identify issues quickly. Detect and resolve specific problems using our integrated torque monitoring system, including under- or over-fastened parts, bearing debris, lack of lubrication, out-of-tolerance components, and broken/missing parts.
CONTACT US TO DISCUSS YOUR TORQUE TESTING APPLICATION
Torque testing measurement and analysis across your production line
Below are just a few examples of how we've helped manufacturers add measurement and analysis capabilities to their torque operations for better insight and defect detection:
Torque testing electric motors
Torque testing is a critical part of the functional test of an electric motor. Sciemetric’s solution identifies faulty motors based on ‘High Potential’, ‘Minimum Start Voltage’, ‘Pull-up Torque’ and ‘No-load’ tests. Key components of the testing and the related waveforms include:
- Rotary testing
- Encoder sampling
- Torque signature vs. angle
- Current testing
Short block torque-to-turn testing
A major engine manufacturer was experiencing customer complaints and costly warranty repairs. They needed an accurate and reliable solution that could detect defects early in the Short Block assembly process, specifically defects caused by crankshafts.
Sciemetric’s Short Block Crank Torque- to-Turn test measures the torque as the crank is rotated. This torque monitoring and analysis system uses advanced algorithms for consistent and reliable detection of defects such as contaminated bearings, debris, incorrect fit, bent or nicked cranks, etc.
Identify defects on nearly any torque application on your production line
- A/C compressor
- Ball joint
- Wiper torque
- Starter torque
- Seat track
- Window torque
- Rod connections
- Tight bearings
- Head and cam
- Crank torque to turn
- Pinion nut
- Ring gear run down
- Bolt fastening
- Screw quality
Read more about the basics of torque testing from our experts in the pages of Assembly Magazine >
CONTACT US TO DISCUSS YOUR TEST
Real-time, continuous torque process monitoring systems from Sciemetric catch more defects
Catch production problems in real-time with Sciemetric's in station part test and process monitoring and data acquisition systems.
On many production lines, fastening and run-down operations are monitored only for verification that a specified torque was reached. Our torque testing systems go far beyond this basic pass/fail determination to monitor and collect data from every millisecond of the process using digital process signatures. This level of torque monitoring and analysis provides much more granular and effective defect detection. If it takes longer than usual to reach a specified torque or requires more or less force, your team will know in real-time.
Sciemetric offers two solutions for monitoring and analysis of your torque testing operations: sigPOD and Sciemetric EDGE. Each solution applies the power and insight of proprietary digital process signature technology, combined with the hardware to suit your needs on the line. See below to discover which solution is right for you.
sigPOD
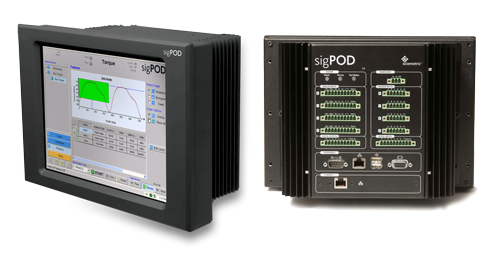
The sigPOD is powerful process monitoring platform that offers an in-station display to be able to easily view and analyze your basic test data using PSV right at the station.
Manufacturers prefer this option for applications requiring several channels of synchronous data collection for complex tests. This would apply to areas of your line where you are monitoring multiple parameters along with your torque operation. One example is engine cold test and other functional engine testing, with multiple sensors would be monitoring at once to get a full picture.
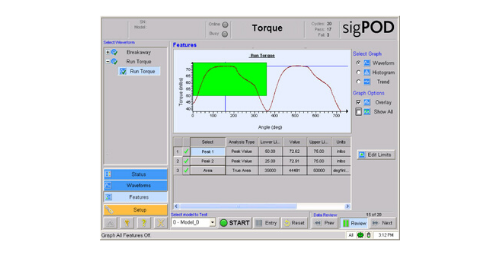
Sciemetric EDGE
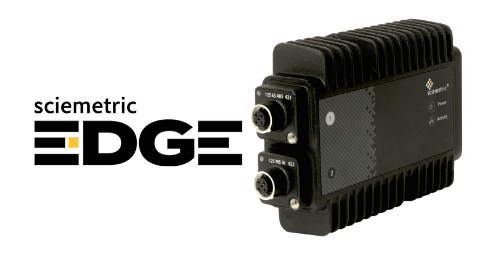
The Sciemetric EDGE is an innovative platform for torque test monitoring and control. Its compact, modular design allows it to be easily integrated onto your line and offers remote access control.
This model is preferred for standard two-channel torque applications, offering simple integration and blazing fast cycle times. The platform delivers advanced data analytics information to your industrial PC, allowing you to maintain efficiency of your operations on the factory floor or in the field.
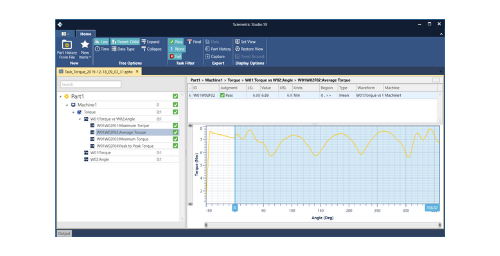
Consolidate production data from multiple stations for better visibility
Fastening and rundown stations often have monitoring solutions provided by the tool supplier. The valuable part data collected by these systems often reside in silos. Sciemetric’s QualityWorX enables manufacturers to store all part data from across the assembly line into a centralized database. Unique manufacturing analytics software allows the analysis of the waveforms, comparison and correlation of stations and more.
GET A QUOTE ON TORQUE TEST DATA FOR YOUR PRODUCTION LINE