The Sentinel Blackbelt Pro™ manages and executes 4-part tests synchronous or asynchronous, at different stations, and all under the control of one Blackbelt Pro instrument.
Advanced Product Features
- Wall mount configuration 16.25” W x 13.5” H x 10” D
- Benchtop configuration 11” W x 12.5” H x 17” D
- Powerful 32-bit processor & (8) 24 –bit A/D converters
- Language neutral color LCD, 9.25” touch screen, 480 x 272 operator display
- XY Graphing (pressure, loss, or flow)-English, Chinese, Korean, Spanish
- Expanded instrument control through EtherNet/IP™ communication
- On-screen test status identifies Pass/Fail/In-test/Error
- Benchtop has independent port LED Pass/Fail; lighting
- Barcode ready input RS232 Alpha-numeric string stored with test result.
- Modular pneumatic and control packages
- Single test channel
Standard Features
- Auto Calibration includes mass flow leak standard certified for pressure and flow
- Transducer zero and span are automatically reset during auto calibration
- “Performance factor” calibration feedback ensures accurate results
- Self Test isolates the test instrument pneumatics to verify a “no leak” condition
- Features ensure accurate results and easy operator setup and troubleshooting
- Firmware validation document included
Standard Test Pressure Ranges
Standard pressure transducer, valve manifolds, and regulator ranges:
-14.5, -2, -0.1 to 4”HG, 0.5, 2, 30, 100, 200, 400, 500 (psig) with electronic regulation
- Std. Cv flow valves and test manifold available up to 100 psig
- High Cv flow valves and manifold available up to 200 psig range allows 5 times faster fill and exhaust to reduce cycle times on large parts
- Low volume (0.07cc) manifold available
- Absolute pressure transducer
- Six point pressure calibration
- Data resolution 0.00001 psi/ and scc/m.
- Optional electronic regulator available with multi-point calibration
Mass Flow Sensor Ranges
CTS will optimize the flow sensor & flow range per application.
Contact Application Engineering for available mass flow sensors.
Standard delivery range:
- 0.5 – 50 scc/m
- 2.0 – 250 scc/m
- 30 – 3000 scc/m
- 2, 30, & 100 psig
Selectable Test Units of Measure
- Pressure: PSIG, PSIV, inH2O, cmH2O, mmH2O, kg/cm2, ATM, inHg, cmHg, mmHg, kPa, Pa, MPa, Bar, mBar, Torr
- Flow: Sccm, sccs, scch, slpm, slps, slph, s
- Time: Sec, msec, min
- Units of measure can be instrument global or per test program
Tooling Control
- 18 inputs/18 outputs with programmable tooling motions with feedback
- Part marking control
- Tooling I/O is externally connected
- I/O 24 VDC – I/O cables supplied with instrumentation
Test Data Storage
- 1 million part test results including Date / Time / Barcode / Test Results
- Selectable part serialization in the test data stream
- SPC data tracking for part traceability
- Expandable download through USB port
Electrical Requirements and Connectivity
- 88-264 VAC, 47-63 Hz or optional 22-26 VDC
- RS232(2)
- Telnet (2), EtherNet/IP™ communication
- Email Alerts
- “SmartKey” Digital ID for 21CFR Part 11 tracking
- Barcode ready (RS232)
- Mobile text
- (3) USB mass storage device for backup, restore, and reports (FAT32, USB1.0,1.1,2.0)
- ¼” Colder fitting for test line attachment
Testing Technologies
Multi-port, Multi-test, Multi-Channel; Configurable for Leak, Flow, Pressure, and Vacuum Test Requirements
- Pressure/Vacuum decay-pressure change
- Pressure/Vacuum decay-with certified leak standard
- Pressure/Vacuum decay-pressure change/time
- Occlusion test (vacuum or pressure test)
- Mass flow direct flow reading
- Mass flow with certified leak standard
Instrument Highlights
- This instrument is highly configurable and very flexible
- 4-port independent, synchronous and asynchronous test capability
- 1, 2, 3, or 4 port sequential operation
- Multi-test dependence programming
- Store up to 999 part programs
- 200,000 test sequencing
- Recall up to 1 million test records from internal memory
- Provide digital I/O control 18 inputs / 18 outputs with enhanced Tooling Control
- “SmartKey” digital ID for 21CFR Part 11 tracking
Selectable Test Parameters
- Quick Test
- Test Pressure Level Compensation (selectable on/off)
- Adjustable Environmental Drift Correction per test program
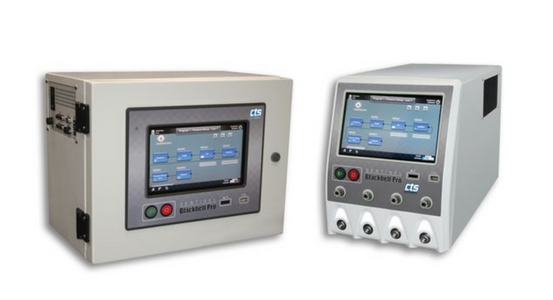