Detect defects in press-fit or joining operations
Leaks, unwanted noise and other defects found downstream on production lines are often due to missed issues during the press-fit process.
Upgrade your press-force monitoring system with advanced digital process signature technology designed to catch defects accurately and reliably as they occur. Monitor every step of the press force operation and perform real-time analysis to continuously improve manufacturing and achieve higher productivity.
See how a press force monitoring system measures force displacement using force vs. time, distance vs. time and force vs. distance. Sciemetric CTO Richard Brine also explains how waveforms provide greater measurement accuracy.
Typical defects and quality issues found during press force and press-fit operations
The application of a press-fit monitor will help to identify these typical problems that result in defects. Deploy a real-time force monitoring system with any hydraulic, servo electric, pneumatic (air over oil), or mechanical presses.
Find part issues
- Incorrect orientation
- Cracked
- Over-size
- Under-size
- Improper insertion
- Tolerance stack-up
Spot machine issues
- Bad alignment
- Improper lubrication
- Wrong ram speed
- Loose fixtures
- Damaged seals
- Low hydraulic pressure
CONTACT US TO DISCUSS YOUR PRESS APPLICATION
A few examples of how Sciemetric has helped manufacturers apply press-fit monitoring to improve product quality
Create a new integrity test system that included press-fit monitoring for a reputable brake pad manufacturer
Replace subjective method of testing rubber-to-metal bond on a part
Provide precise control and monitoring of power steering pump press-fit assembly for an automotive parts manufacturer
View more press-fit application notes
Digital signatures provide greater accuracy in press force monitoring
Sciemetric force distance monitoring technology is based on digital process signatures, or waveform analysis, which analyzes all the critical points of an operation to determine a pass/fail decision. Signature analysis provides a visual representation of the process.
The force distance waveform is a combination of force vs. time and distance vs. time measurements.
The combined press signature provides a visual overview of the key measurement parameters.
Variations in the repeatable curve are indications of problems. Only Sciemetric enables the reprocessing and overlay of signatures to determine the root cause of issues. For example, looking at a population of signatures, the chatter seen can be attributed to spikes in force caused by the rocking of the pin being inserted during the operation.
More on digital process signatures
Flexible press-fit monitoring solutions to fit your needs
Unique digital process signature analysis software allows you to capture, analyze, and store thousands of data points. Collecting insights from each force distance operation delivers the most accurate, real-time defect detection. With Sciemetric, you can view your reports in real-time or compare results later to improve production efficiency. We can help you determine the right approach for your test!
sigPOD
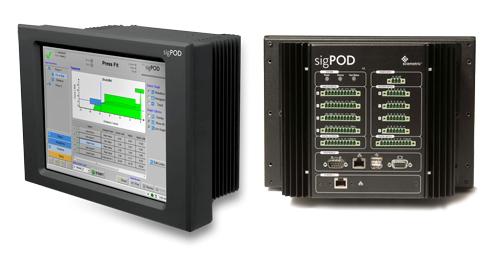
The sigPOD is powerful process monitoring platform that offers an in-station display, intelligent limit setting, reporting and much more.
A pre-configured template for press-fit monitoring is provided at no cost!
Sciemetric EDGE
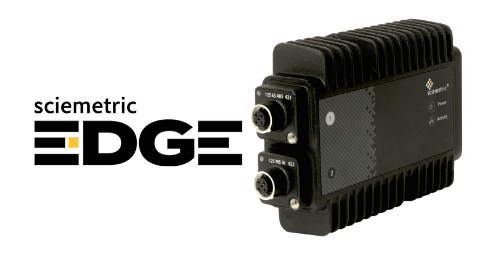
This innovative platform offers a compact, modular design and remote access control for process monitoring and control throughout your production line. Managed with Sciemetric Studio manufacturing analytics software, Sciemetric EDGE can be applied on a per ram basis, close to the operation for seamless integration with your system.
Smart manufacturing: Lever the data from your press force operations
Our press-fit monitoring systems enables manufacturers to use the data from press force operations for continuous process improvement. The system also allows you to connect press operations to other operations in the factory to provide a complete part history.
Explore how our QualityWorX suite of data management and manufacturing analytics software can consolidate press-fit monitoring data your other production part data, enabling quick response to quality or throughput issues. Find the root causes of defects, correlate downstream problems to upstream stations and get full traceability.