Take your favorite sport—hockey, soccer, baseball. A contentious goal or run is scored. Officials go upstairs to for a review of the play to decide if it will count. What will provide the strongest evidence to support their decision—a video instant replay or snapshots of a few isolated points in time?
It’s the replay, of course. Your production line can deliver this same level of actionable insight, with digital process signature analysis (also known as waveform analysis).
What is a digital process signature?
A signature is a visual representation of everything that happened to a part during a manufacturing operation. Every very process has a repeatable signature or digital “fingerprint” when compliant and under control.
Signatures are created from data collected by sensors such as load-cells, temperature, position and pressure sensors, microphones or displacement gauges at the station. The signals can be physical measurements or computed values such as horsepower or efficiency based on specific measurements and mathematical formulae.
The digital traces represent hundreds or thousands of data points which are used at the station to provide a much more accurate pass/fail decision. The rich data is collected and can later be mined to resolve issues quickly or optimize production. Sciemetric pioneered digital process signature analysis for use in manufacturing in the 1990s and remains at the forefront of innovation in the technology in industrial applications.
What you can learn from a digital process signature analysis?
What can a signature tell you? Take press-fit monitoring, a common manufacturing operation, for example.
Digital signatures visualize as a waveform that combines force vs. time and distance vs. time measurements. This casts a spotlight on a number of possible issues with a part, as well as issues with the process or the machine. Any of these could result in a flawed pressing operation that leads to downstream defects.
.
Catch what other test and monitoring systems miss
Other test and monitoring systems catch defects later in the manufacturing process. That means you might not notice issues until the parts are fully assembled and ready for shipment. Digital process signature technology provides the most accurate measurement at the station level to provide a picture of part and process health.
Our pass/fail test analysis delivers greater accuracy and better visibility than other methods and provides easier interpretation using visualized data. Use digital process signature analysis on virtually any manufacturing process for improved monitoring throughout your entire production line.
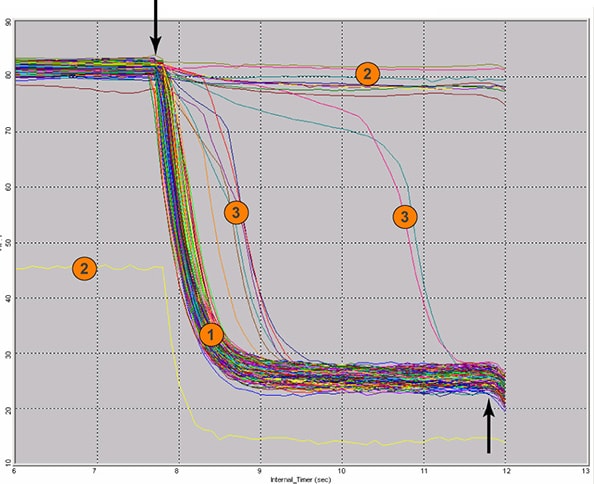
2: Obvious failures caught by any system.
3: Subtle failures that are missed by other systems because they meet the minimum criteria for a "pass".
These anomalies can point to process issues and/or problems with parts down the line.
Scalar data tells only part of the story
Most manufacturing data management systems collect scalar data only, limited to a few data points for each cycle of a manufacturing process or test—a handful of snapshots. This is sufficient to monitor and track the health of a production line or provide baseline traceability. But when problems arise, it just isn’t enough to quickly find and address the root cause.
For Industry 4.0, front-line quality and manufacturing engineers and operators need the right data to help them resolve issues quickly — increasing yield, cutting scrap and rework rates, improving station performance, and reducing downtime due to defects. Sciemetric’s manufacturing analytics technology, using digital signature process analysis, reveals real-time data and insights throughout your production line to help you optimize all your test cycle times, resulting in increased efficiency and profitability.
Read this blog, SPC Can Catch a Problem, But Only Signature Analysis Can Fix It Fast, to learn more.
How does digital process signature analysis
provide traceability in manufacturing?
Sciemetric is the only company that enables in-depth, real-time analysis and visualization of digital process signatures in manufacturing. Our digital pass/fail analysis tools allow users to overlay and compare digital signatures in large or small populations—from thousands of parts right down to a single part history.
According to our customers, industrial process analysis the fastest way to access and view complex data to:
- Provide Traceability: Quickly determine the “how” and “why” of any issue that is affecting quality or compliance with customer requirements or regulatory standards.
- Trace Root Cause: Dramatically improve defect avoidance and contain defects for a fraction of the cost of a day of lost production.
- Improve Quality: Isolate potentially defective products by serial or batch numbers based on specific process signature symptoms, or desired build parameters.
- Increase Output: Overcome barriers to increased output, whether it’s related to unexpected downtime, poor FTY/FPY/FTT, or test stations that need to be optimized to keep pace with production.
- Speed Runoff: Diagnose and address issues with calibration, alignment, pressure, angle and other parameters, to launch new machines and new lines faster.
Read our e-book, How to Put Your Manufacturing Data to Work, to learn more about using digital process signature analysis for improved traceability in manufacturing.
Watch Sciemetric CTO Richard Brine explain how manufacturers can use signature analysis to improve leak testing and more in this video segment with Quality Digest Live.