Contributed by: Sciemetric Staff
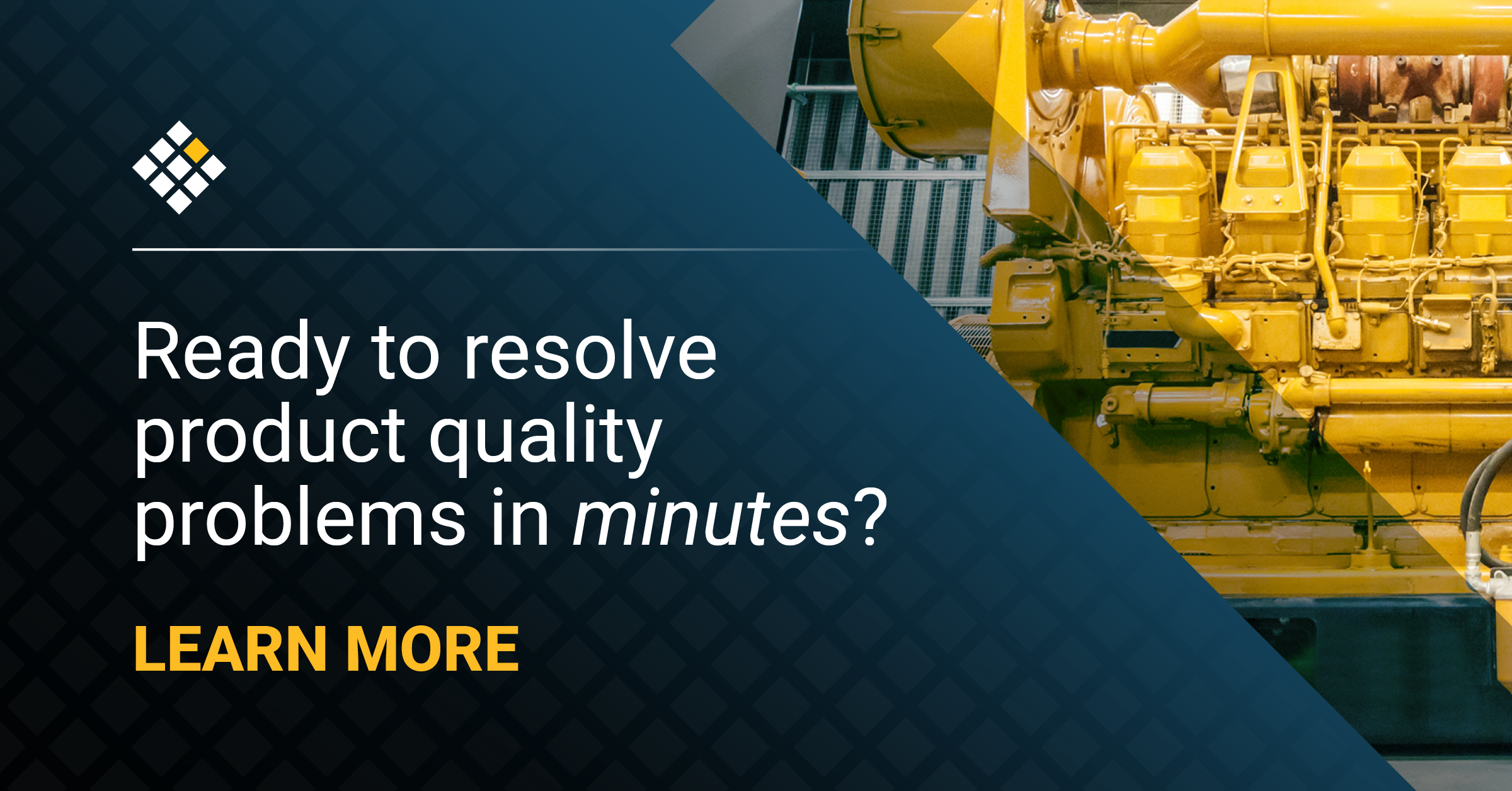
When quality issues halt production, the ability to retrieve and analyze data quickly to trace root cause becomes invaluable. Having a good data management system in place can save manufacturers hours, days, or even weeks in costly downtime—not to mention improve product quality.
In one specific case, we helped an OEM (a manufacturer of agricultural machinery) achieve faster root cause analysis, higher yields, and improved product quality—all by making better use of the data they were already collecting on the production line.
The problem came down to poor data management
When confronted with a quality issue, it would routinely take this manufacturer as long as a week to retrieve all the related station data scattered across the plant to analyze and identify the issue. And while they were searching for the problem, they didn’t want to take the risk of continuing to ship potentially defective products, leading to uncertainty and lengthy (costly) production delays.
Ultimately, their problem came down to poor data management and accessibility across their plant floor. They were collecting data, but it was not accessible in a way that would help them solve their problems in the event of a quality issue.
We identified the below top problems with their data management system:
- Data was not accessible in one place, with data trapped in silos across the plant floor
- Data was not accessible in one common format, making it difficult to compare
- Custom query tools were required for each data retrieval—a timely guessing game
- No simple, standardized data reporting and visualization tools
How Sciemetric made better use of their data
Using QualityWorX, Sciemetric’s data management software, our team of engineers implemented the following changes:
- Custom scripting to convert data from all processes to one common format
- Custom algorithms for easy data retrieval/analysis
- Clear, visualized reporting tools
- Standardization across the enterprise
Sciemetric’s data management tools are flexible and agnostic, able to communicate with other third-party process and test station equipment and operating systems, which made it easy to connect and collect data from different processes across their production line.
Our engineers took all the manufacturer’s disparate forms of process and test data from the line and converted it into formats that could be uploaded into the QualityWorX database. Data was no longer trapped in silos. With one common database and a common data format, the manufacturer could now pull a full birth history for a part or unit by serial number.
Equipped with a new suite of algorithms to quickly search, retrieve and correlate data from this single centralized repository, the manufacturer’s quality teams were now able to achieve fast and accurate root cause analysis.
The results of these data management updates
After implementing the above changes in their production process, this manufacturer cut substantial downtime from their root cause analysis process. Production and quality issues that once took this manufacturer days or weeks to identify and address could now be resolved in minutes!
Sciemetric’s manufacturing analytics tools have allowed the manufacturer to quickly drill into its data and analyze the impact of design changes, improve quality checks and report on metrics. All this has been achieved from the data the manufacturer already collected—it just needed the right data management and analysis tools to unlock its potential.
This new data management strategy performed so well in this plant that the manufacturer then adopted QualityWorX data management as a standardized quality platform across four plants in North America and Europe. Want to learn more? Download the application note for the full story
Interested in how your production data could be helping your throughput and product quality? Contact the data experts at Sciemetric!