Contributed by: Sciemetric Staff
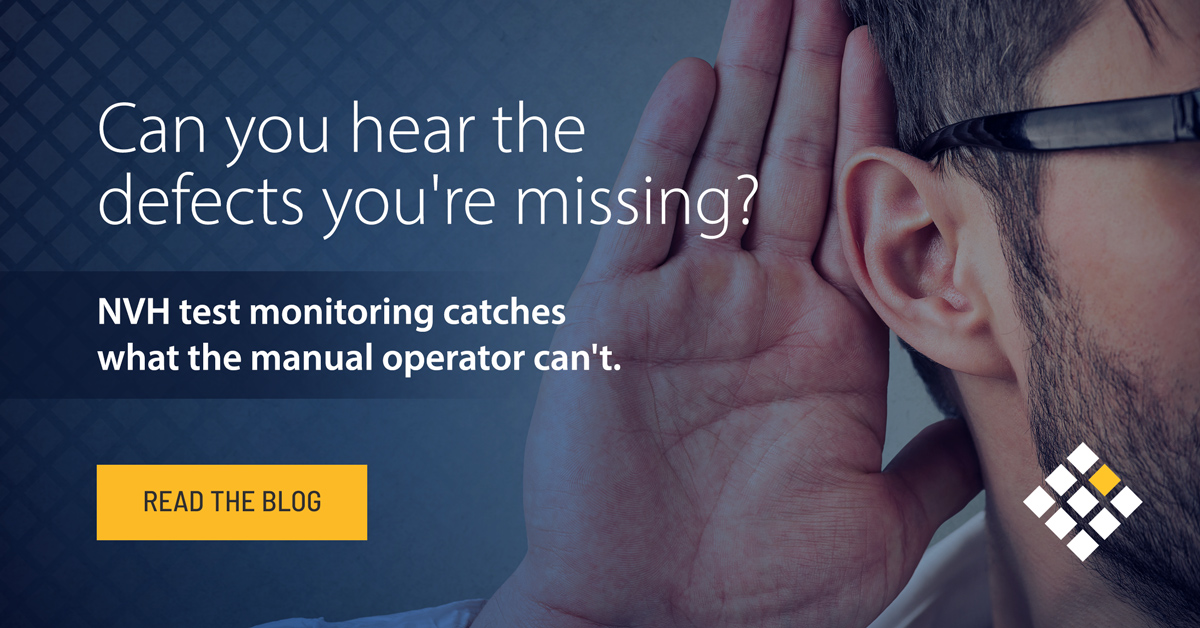
Snap ring installation is an important part of axle function in vehicles. If the snap rings on an axle assembly are improperly seated, it can cause vibration issues or even the disconnection of the axle shaft during operation.
The reason why problems with snap ring applications often go unnoticed until the vehicle assembly floor, or a problem in the field, is that the conditions and function of the installation are challenging to monitor without the right tools.
We worked with an automotive manufacturer that was having major problems with their axles, resulting in warranty claims, production downtime, and rework costs. The problem was traced to the snap ring installation station. Sciemetric’s NVH (noise, vibration, harshness) monitoring solution provided them with accurate, reliable snap ring verification, catching any faulty parts before they moved further down the line. Here's how:
Adding automated measurement and analysis to snap ring installation station for consistent, reliable pass/fail results
Many manufacturers rely on manual methods of quality control during the snap ring application process, but the conditions of the process can make it very difficult to get a reliable pass/fail result using manual methods.
The particular manufacturer we were working with was using a combination of machine vision and manual operator monitoring. However, with so many problems being found down the line and in the field, this manual defect detection technique wasn’t working.
This manufacturer’s snap ring installation station had two phases of operation. The first phase of the station was externally visible and often (though not 100% of the time) able to be monitored using a machine vision camera to confirm correct placement. However, the second phase included snap rings securing the inner bearing race to the axle shaft and the outer race to the housing. In both cases it is impossible to insert a camera, making machine vision unusable. Instead, they had a human operator manually listening to confirm the two ‘click’ events as each snap ring was seated into place.
Unfortunately, what made this particularly hard to reliably monitor with the human ear is that these two snap events were happening within a tenth of a second of each other. With the surrounding noise on the manufacturing floor, these two distinct but necessary ‘click’ events of the snap rings seating into place become almost impossible for a human operator to reliably detect.
To fix the manufacturer’s problem, Sciemetric provided a way to take out the guesswork for the second phase of the operation, adding automated measurement and analysis to snap ring installation station for consistent, reliable pass/fail results.
NVH monitoring and signature waveform analysis provide accurate, reliable pass/fail results
Sciemetric’s solution was to measure press and vibration during the snap ring application processes, allowing the manufacturer to reliably detect the audible ‘clicks’ as each snap ring engaged into their proper seated position. Sciemetric used a draw-wire distance sensor and mounted accelerometer to measure the events. Using Sciemetric software, this data was then processed into signature waveforms for simple visual analysis (see screens below).
By comparing signature waveforms of known bad parts to those of good parts, it became possible to match up the precise timing of good vibration events. Seeing the right waveform spike (‘click’) at the right place/time during the process confirmed it was a properly seated snap ring. NVH monitoring combined with signature waveform analysis provided an accuracy that manual verification methods couldn’t deliver.
Sciemetric’s solution enabled a consistent, reliable pass/fail reading at the station and offered the additional ability to better identify, analyze, and solve future problems that could arise.
To learn more about how Sciemetric solved this manufacturer’s problem with snap ring verification, read our application note >
CONTACT US TO DISCUSS AN APPLICATION
CAUSING PROBLEMS ON YOUR LINE