Contributed by: Sciemetric Staff
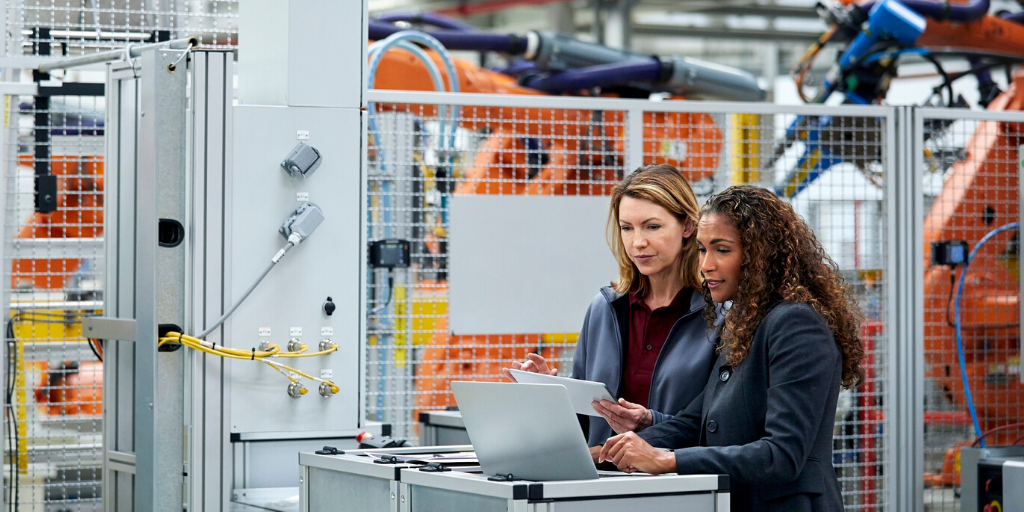
Should the focus of a discrete manufacturer be on overall yield/output, or on first time yield?
Before we address the question, let’s define the difference.
The difference between overall yield and first time yield (FTY)
Overall yield is the total final output of a manufacturing line. It includes any units that had to be reworked in a repair bay due to defects or errors but did end up earning the stamp of approval.
First time yield (FTY), on the other hand, looks only at those units that made it all the way down the line and out the door without any defects or errors that required rework.
So the question becomes – does it provide a better return to invest in improving overall yield (which includes the time/cost of reworking faulty units) or to invest in FTY, to reduce the number of units that prove faulty in the first place?
Obviously, the answer depends on how high of a rework rate is hidden in a manufacturer’s overall yield figure, and how much the rework adds to the average production cost per unit.
LOOKING TO IMPROVE FIRST TIME YIELD? LEARN ABOUT SCIEMETRIC'S APPROACH
An example:
The cost per unit is $5,000 – $2,500 for the materials and $2,500 for the transformation costs. The annual target production run rate is 10,000 units. Say the FTY is 90 per cent. If the manufacturer does not re-work the failed units, then 11,112 units must actually be started to achieve the target output of 10,000. This results in $5.6 million in scrap – millions of dollars wasted, every year. This increases the product costs from the raw, unyielded value of $5,000 to an actual value of $5,556 per unit.
Then the manufacturer implements a re-work process that recovers 80 per cent of the failed units. This boosts overall yield from 90 to 98 per cent (note that FTY remains at 90 per cent). The cost of the re-work is 50 per cent more than the initial transformation cost – $3,750. This appears to be a worthwhile investment considering $5,000 has already been committed to the failed unit. But consider that total rework costs amount to $3.8 million per year. This boosts total average production cost from $5,000 to $5,485.19 per unit.
Now, what if FTY was raised from 90 to 98 per cent – hitting the same yield without the cost of rework?
The total average production cost per unit would be $5,102.04, for a total savings per part of $383.15, or about $3.83 million in total per year. Of course, the trick is how to make the productivity improvements that will drive this increase in FTY. Worthwhile gains in FTY that will save millions of dollars a year can be achieved with investments of only a few hundred thousand dollars.
How is this possible?
It begins by making a digital connection with each station and capturing the right kind and the right depth of data from every process. Then using a centralized data management platform to integrate all this data into a single database where it can be analyzed, cross-referenced and visualized to support rapid and sound decision-making. This is digital process signature analysis.
It doesn’t have to be a huge increase for the ROI to exceed the cost of rework. Take the above example again – increasing FTY by even two percentage points, to 92 per cent, would still generate costs savings greater than from boosting total yield to 98 per cent through rework.
The pressure is on like never before to cut production costs and drive quality, and yet, many manufacturers still focus on overall yield when it is FTY that offers the most benefit to their bottom line. By using process signature analysis, substantial FTY gains can be made that make it well worth the investment.
LOOKING TO IMPROVE FIRST TIME YIELD ON YOUR LINE? LEARN HOW SCIEMETRIC CAN HELP