Contributed by: Sciemetric Staff
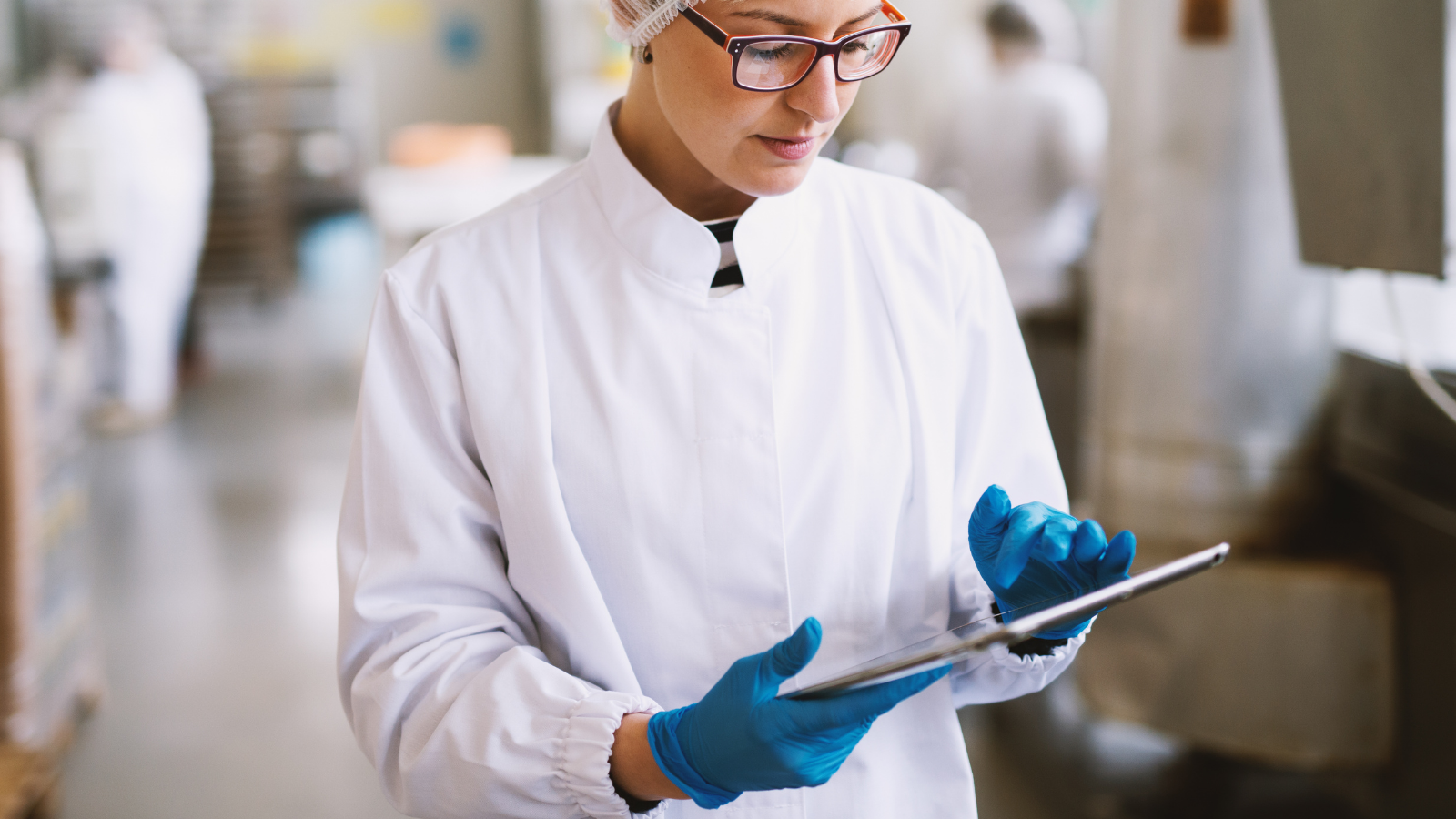
Paper-based data management and reporting workflows tend to limit the line’s capacity and scalability, and are prone to manual error. When these workflows start creating noticeable bottlenecks on your line, it’s time to look for a more streamlined solution.
Determine your needs
The first thing you need to consider is the scope and scale of your needs. This may lead you to opt for a transitional step by having line operators continue to manually record a test, quality reading, or process data on the floor before submitting it to a digital form (whether that is via a wireless tablet or a connected PC).
Depending on the speed and volume of your production line, this may be an adequate solution, at least for your present needs. However, while this will certainly provide streamlined data management and quicker access to records, the downside of maintaining manual data entry methods is that your data continues to be vulnerable to issues related to accuracy and scalability as your yield increases.
Weigh the benefits: Cost vs. ROI
You’ll need to weigh the benefits of your options: the benefits of investing in a fully automated data collection and management solution from the beginning, versus maintaining manual data entry.
- It is important to consider that though a fully automated workflow may require a more substantial investment upfront, the benefits you experience in the long-term will far outweigh the cost. In fact, one manufacturer we worked with estimated that eliminating manual paper processes, applying an automated data collection solution, would reduce costs per plant by $2 million to $3 million a year.
Employing the right digital tools and workflows for your line will ensure reliable, validated data is delivered straight to a central database from any measuring device, test stand or quality assurance process. This breaks down the data silos that prevent your team from fully understanding, in production real-time, what really is happening at every step of production.
Consider an integrated data management and analytics solution with real-time defect detection and alerting capability for the full benefits of automation
Once you have an automated workflow in place, delivering all of your production data to a central database, enabling a manufacturing data analytics solution that detects defects and alerts you in real-time will allow you to fully realize the benefits of an automated workflow, ensuring continuous monitoring and defect detection.
With Sciemetric Studio 2.0, for example, your team can enable statistical process control (SPC), based on Nelson rules, that checks your process data for potential rule breaches, or create alerts for continuous real-time data monitoring. When a quality check is missing the mark or a process is not performing within set limits, an alerting engine will capture the data, log the incident and can also send an email alert.
The benefits of applying automation and manufacturing analytics in one common solution
The advantages of employing this kind of automation and analytical intelligence to your line far outweigh any perceived benefit from clinging to outdated manual process.
Benefits include:
- Improved quality, less scrap: Faster and more accurate capture of defects to avoid piles of scrap or rework.
- Increased reliability: The likelihood of human error is drastically reduced.
- Supply chain integrity: Optimize the first-time yield of the line and catch any issues with supplier sub-components before they enter production.
- Defensible results: You gain a data-driven audit trail with which to verify where responsibility for a quality issue rests – with your operations, with a supplier or with the OEM (if you are a supplier to an OEM).
See how one manufacturer eliminated bottlenecks and enabled yield increase with switch to digital records
This maker of implantable medical devices eliminated a costly production bottleneck related to quality inspection, and increased its yield to meet soaring customer demand, by switching to digital records. The manufacturer was also able to automate defect detection and quality control using Sciemetric Studio's SPC-enabled real-time alerting engine. See how these benefits could be applied to your line, too!
Want to learn how data collection and analytics could be applied to improve processes and defect detection on your line? Contact us to discuss, or request a demo.