Contributed by: Sciemetric Staff
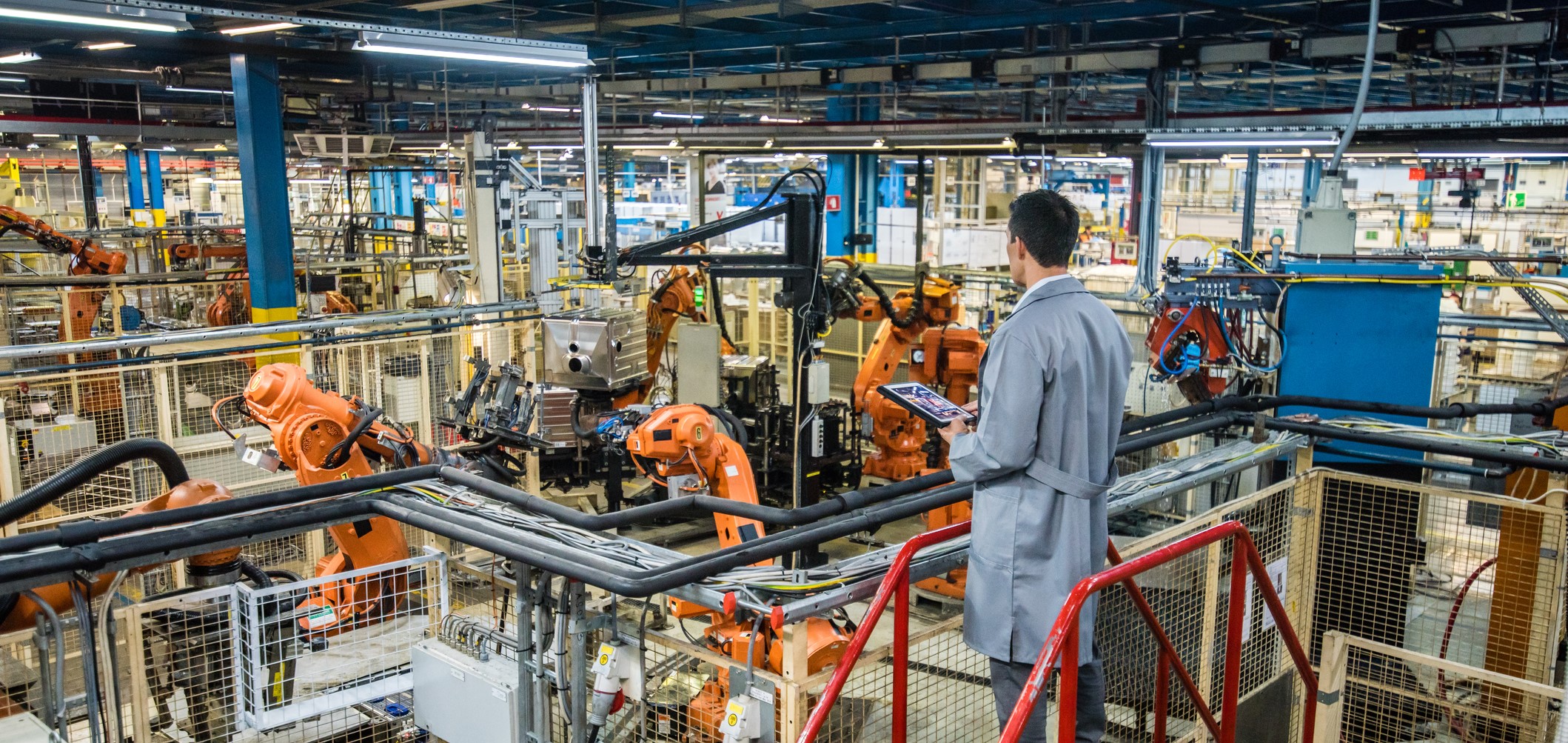
If you look across any given plant floor you’ll see a large array of different test and monitoring and data acquisitions systems at work. The challenge in implementing, using and maintaining such a disparate set of hardware and software to monitor the line causes a lot of headaches for manufacturing and quality engineers.
There is a tendency to think about the line in terms of individual process, with separate solutions for force-distance monitoring, leak testing, torque testing, etc., rather than as a whole—but it doesn't have to be this way. With one common solution, like the Sciemetric's sigPOD, one platform can do it all.
The benefits of commonality on the production line lie in the “5 Cs”: common hardware, common software, common look and feel, common learning curve and common spare parts. It means using one type of test system across the assembly line for evaluating quality at different processes, using the same standard, universal hardware and software interface.
Here's how manufacturers save time and money with a common testing and monitoring solution across the production line.
Reduce implementation time & fix problems fast
Time to market is important for any successful manufacturer and so getting the line working and keeping it up is your priority. You don’t have to take the time to learn how to use, set up or apply a new system. If there’s a problem with the system on the line you are able to swap it out easily with another standard box—it’s that easy.
Save costs and reduce inventory on spares
You don’t need to maintain a vast inventory of spares for all kinds of systems. In a commonality approach, one hardware box can be used for many applications on the line.
Consistent information to help you make decisions
There’s the old line about comparing apples to oranges. Test and monitoring systems often act as data acquisition modules, but they all have their own way of doing it. The data collected is not the same. For example, if one system provides process signatures and the other doesn’t, it makes it difficult to correlate downstream failures to an upstream process. Going with a standard platform means consistency. You will prevent experiencing holes in your data and be able to solve problems much more quickly.
Engineers and operators only need to learn one system
The engineers working on the floor are busy solving problems and getting new lines up and running. Commonality means no learning curve—all the hardware is the same and all the software looks and feels the same, though it is adapted for the application. It also means operators can move from one station to another without extensive training.
Achieving commonality on the line
Is it possible? Yes. Right out of the box Sciemetric’s sigPOD platform delivers on the 5Cs. It not only simplifies management of the line but provides the best test and quality monitoring on the market, helping you produce high quality products and acheive cost savings and optimal defect avoidance. If you are looking at improving the efficiency of your line, consider the commonality approach with sigPOD.