Contributed by: Sciemetric Staff
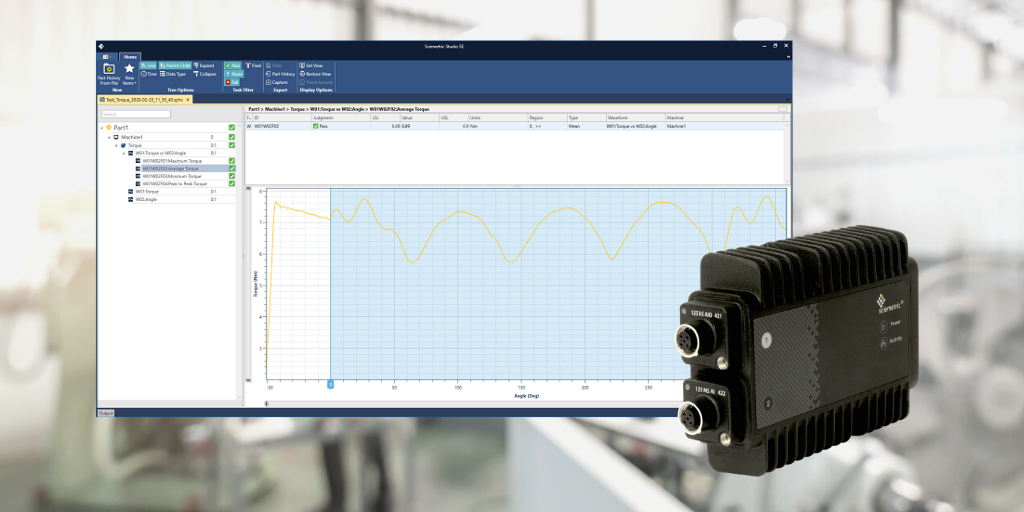
In our first Torque-to-Turn post, we talked about how more data that just maximum or peak torque value must be collected to detect and address possible defects. This applies whether it’s for quality control of fasteners or rotating parts.
This time, we dig deeper into the specific feature checks that should be measured and what they can reveal.
Data-driven feature checks to identify problems during torque operations
Torque testing typically requires a voltage or bridge sensor to measure the torque and an encoder to measure the angle during rotation.
When a torque operation is error or defect free, the values for each of these checks will consistently fall into the same range. When they are visualized as a process signature, the signature will be repeatable. This means that the profile or signature of a “good” torque-to-turn test (or of the installation of a fastener such as a bolt, nut or screw), will be as distinct as a fingerprint.
Any anomalies will show up clearly on the signature as deviations from the established norm. This makes it easy to determine accurate pass/fail in real time. Depending on what feature check or checks are failures, it will help to diagnose the root cause of the problem.
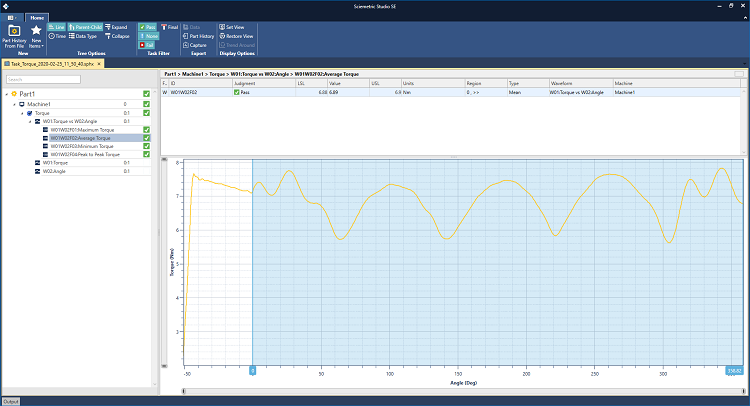
in torque-versus-angle signature to reveal insights into your test.
For example, take a fastener – the entire torque-versus-angle signature is collected and analyzed. The measure of the total rotation angle when the maximum torque was achieved will quickly reveal if mis-threading has occurred. This not only identifies the presence of the compromised fastener, but also the root cause of the defect.
Or the torque-versus-time signature of a crankshaft rotation, with the breakaway torque value extracted as the maximum applied torque before the crankshaft begins to move. If the part displays a high breakaway torque value, the process signature can reveal the cause. For example, if there is debris, this will present as “chattering” in the signature, or if components are misaligned, this will appear as undulations in the signature’s curve.
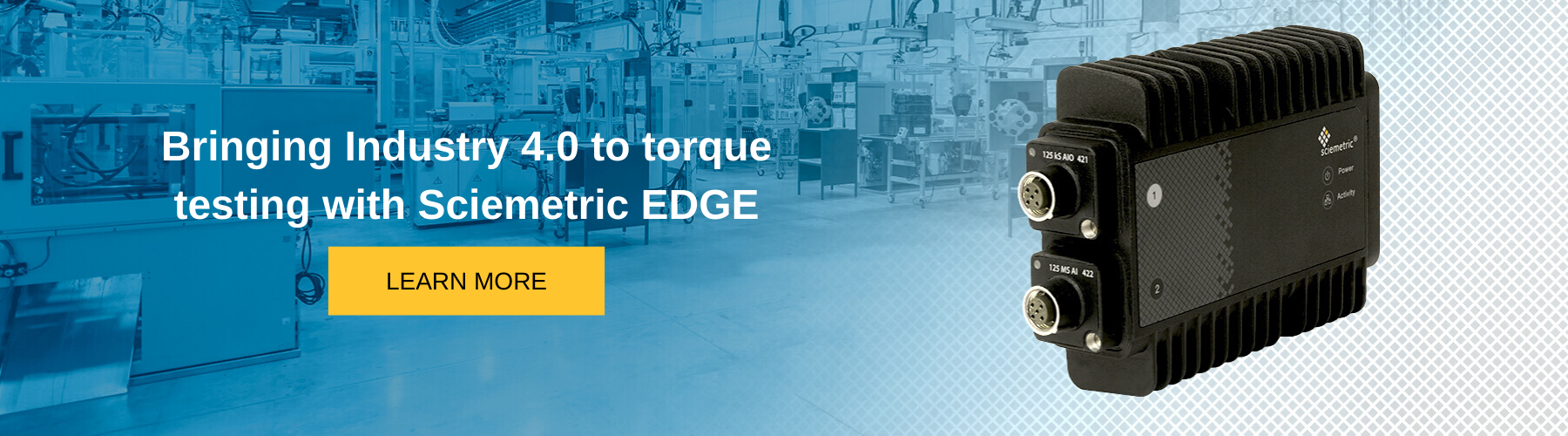
Common feature checks for torque-to-turn tests
Here are the common feature checks for torque-to-turn tests and the defects that are indicated by any deviation from the norm. These feature checks relate specifically to rotating parts such as engines, electric motors, pumps, compressors, transmissions and axles (as opposed to fasteners).
- Maximum Torque: An oversized or undersized bearing or shaft in the case of a breakaway torque test, or also, misassembled parts or poor lubrication.
- Average Torque (mean torque): Damaged parts, out-of-tolerance parts, debris or poor lubrication.
- Minimum Torque: Missing parts, misassembled parts or out-of-tolerance parts.
- Peak-to-Peak Torque: Damaged parts, out-of-tolerance parts, debris or poor lubrication.
By visualizing the signatures of these feature checks, quality issues can be detected in real-time and action taken as early in the production process as possible to contain the costs of scrap and rework and any disruption to the output of the line.
The collective signature data from a press fit station can also be archived and further analyzed. Hundreds, thousands, even tens of thousands of files can be quickly overlaid to spot trends or patterns that may point to issues that haven’t yet led to outright failures.